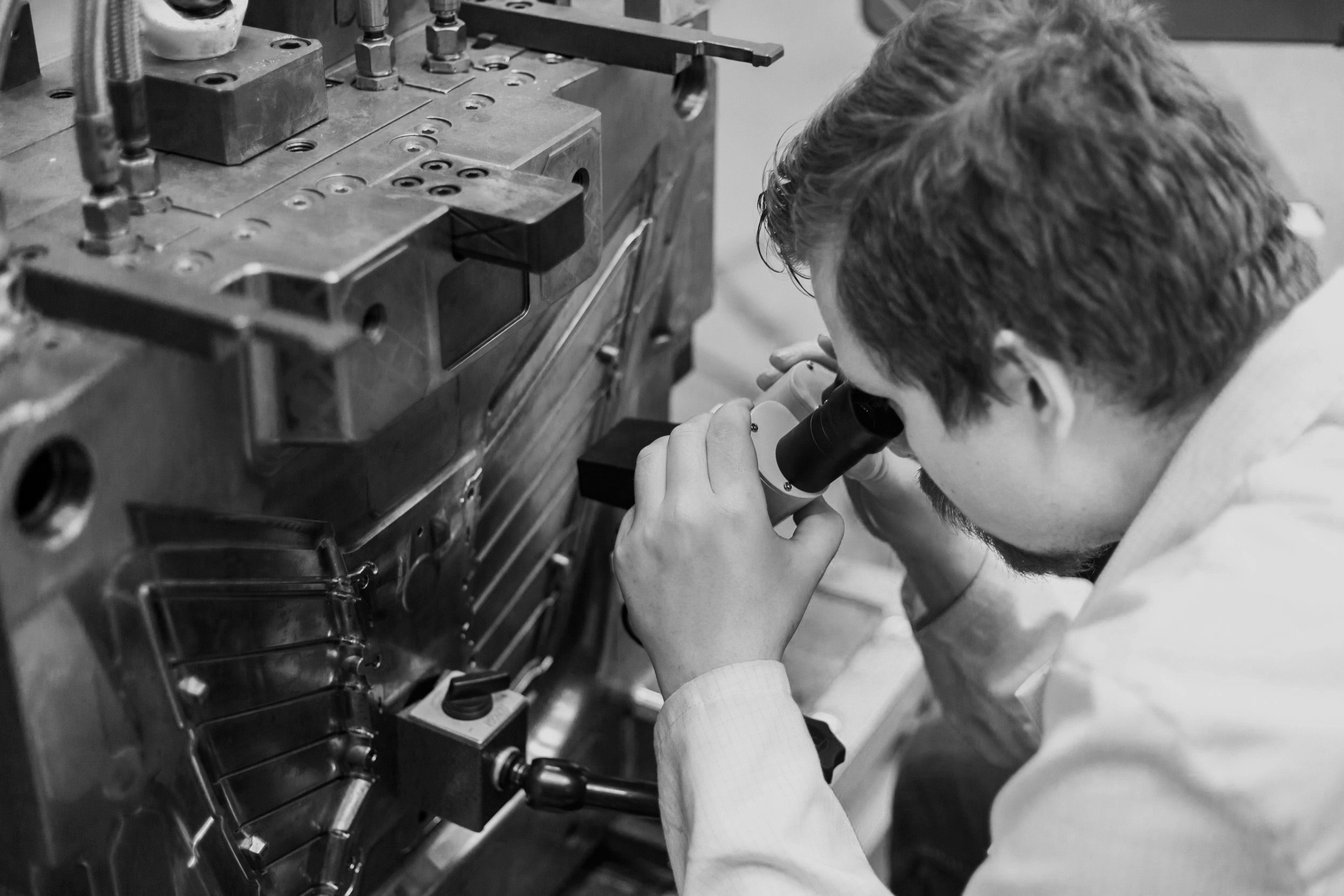
Mould Tooling Services.
✓ Precision Engineered Moulds
✓ Rapid Mould Tooling Services
✓ Aluminium, Steel & Hardened Options
✓ Competitive Mould Tooling Costs
Precision Engineered Moulds
We have been working with our Chinese toolmaking team since the mid 90’s. They consistently produce precision moulds which are, without exception, engineered to a very high standard and have very low defect / down time rates. They are created in such a way that maintenance here in the UK is straight forward with off the shelf components easily available. They are extremely good value even with the air freight costs required to ship them to our factory in Sunbury-on-Thames UK.
Comission A Mould from S.B. Weston
Once a part design is approved we can proceed to the mould tooling phase. On receipt of a CAD file of the approved component, our Chinese toolmaking team will produce a detailed mould drawing showing all aspects and features of the proposed mould. We carefully check this drawing, advise on any revisions, and on approval, the toolmakers will begin the process of manufacturing the mould, or ‘mould tooling’.
How Much Does Mould Tooling Cost?
Mould tooling is the creation of a mould, usually from hardened steel, for the plastic injection moulding process. The cost of mould tooling depends on many factors but most importantly, the size and complexity of the moulded part and the number of moulded parts to be produced simutaneously (in one machine cycle).
We are happy to provide mould tooling price quotations, all we require is a component drawing, CAD file or prototype model to anylyse. If you do not have this we offer a CAD component design service.
How Long To Build A Plastic Injection Mould?
We quote around 90 days for most mould tooling scenarios plus 2 weeks of shipping time from the date of approval of the mould drawing. Towards the end of this 90 day period our Chinese team will run test mouldings which will be shipped to us in the UK for approval. Viewing these test mouldings gives us the opportunity to perform final checks before the final polishing of the mould takes place. If the mouldings are approved, packing and shipping to our factory here in the UK will commence.
UK Mould Tool Maintenance
Injection mould tools are incredibly hard wearing if built correctly but do require maintenance and servicing periodically, especially if they run a lot of hours. We have the facilities in house to perform mould services and replace broken components thanks to the engineering skills of our shop floor team.
Plastic Moulded Part Price Quotation
To confirm a part price we will need to know the type of plastic that the final part will be made from. If you’re not sure - don’t worrry, we can advise on available plastic materials. Having supplied a quotation you will not be under any obligation to proceed, so go ahead, get in contact for a plastic injection mould tooling quotation.
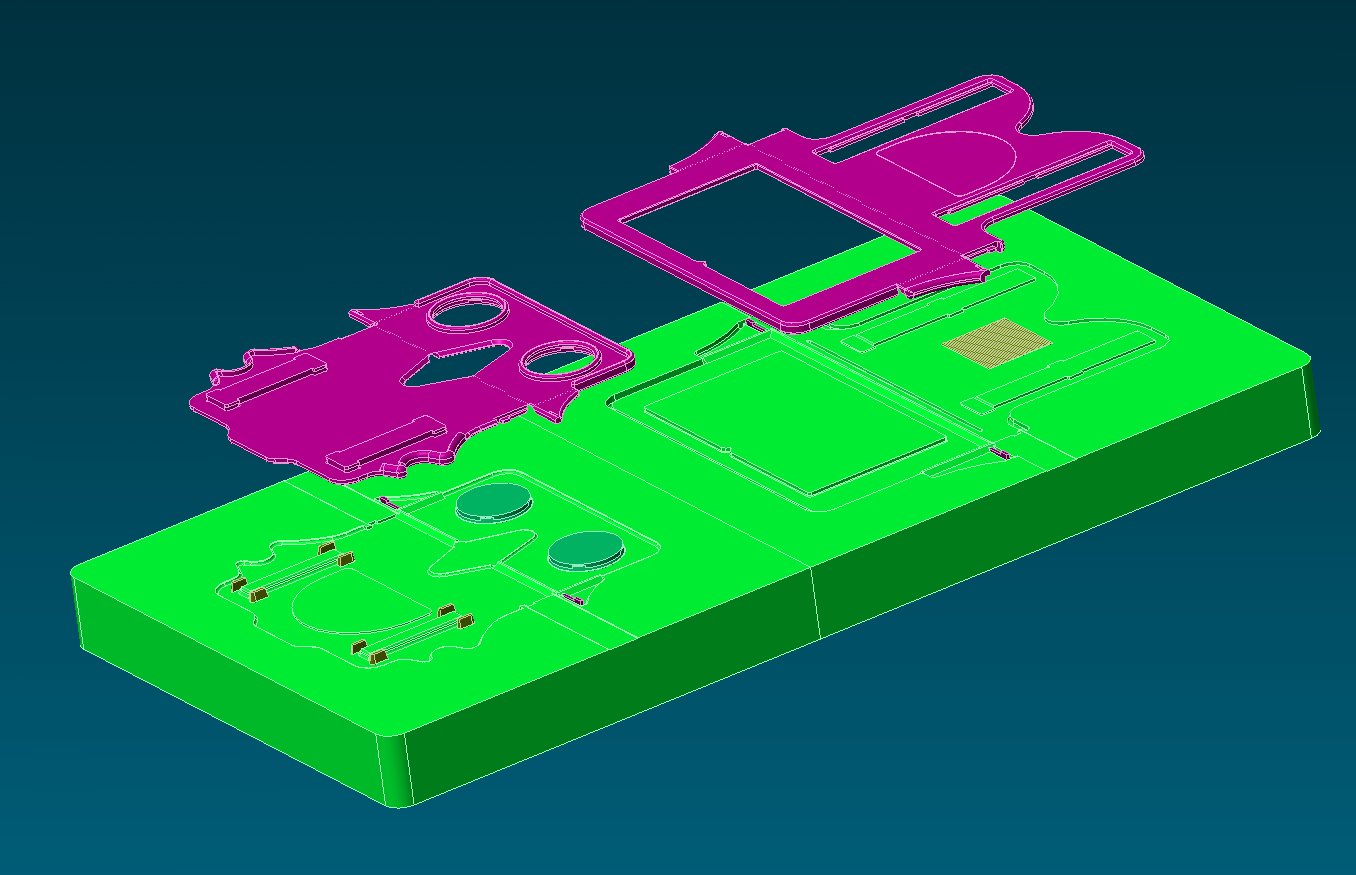
Mould Tooling - The Process.
At the heart of the plastic injection moulding process lies the mould—a precision tool that shapes molten plastic into the desired form. Designing and manufacturing an effective mould is a complex task that demands a keen understanding of materials, mechanics, and manufacturing principles. Below are some of the key design considerations that are addressed when creating an efficient and reliable mould.
1. Material Selection
The choice of material for both the mould and the plastic component is crucial. Moulds are typically made from durable materials like steel or aluminum, chosen for their ability to withstand high pressures and temperatures. The plastic material must be compatible with the mould material and suitable for the intended application of the final product.
2. Mould Configuration
We commission our toolmakers to produce either a single-cavity or multi-cavity mould based on production volume and component complexity. Single-cavity moulds are simpler and less expensive, making them ideal for low-volume production. Multi-cavity moulds, while more costly and complex, significantly increase production efficiency by creating multiple parts in one cycle.
3. Component Design
The design of the component itself influences mould design. Features such as undercuts, threads, and intricate geometries require special attention. Our toolmakers will ensure that the mould can form these features without compromising on part quality or complicating the ejection process.
4. Shrinkage and Warpage
Plastics tend to shrink as they cool and solidify. Our toolmakers predict and compensate for this shrinkage to ensure dimensional accuracy of the part. They will also design the mould to minimize warpage, which can occur due to uneven cooling or stress concentrations.
5. Gate and Runner System
The gate and runner system is the network through which molten plastic flows into the mould cavities. Our toolmakers carefully consider the design of this system to ensure uniform filling, reduce material waste, and minimize cycle times. By running mould flow analysis software on the component, they are able to select the type and location of gates (e.g., pin, edge, or tunnel gates) according to the part geometry and material flow characteristics.
6. Cooling System
Efficient cooling is essential for reducing cycle times and ensuring consistent part quality. Our toolmakers design cooling channels within the mould to remove heat quickly and uniformly. The placement and design of these channels affects cooling efficiency and, consequently, the overall production rate and part quality.
7. Ejection Mechanism
After the plastic solidifies, the part must be ejected from the mould. Our toolmakers design ejection systems—utilising ejector pins, plates, or sleeves—to release the part without damaging it. The ejection mechanism must be synchronized with the mould opening to ensure smooth and consistent part removal.
8. Durability and Maintenance
Moulds are significant investments, so durability is a key consideration. Our toolmakers design moulds to withstand the rigors of repeated use while maintaining tight tolerances. Additionally, they consider ease of maintenance, ensuring that the mould can be cleaned, repaired, and adjusted with minimal downtime.
Contact S.B. Weston for Injection Mold Tooling Services
Creating a mould for plastic injection moulding is a meticulous process that balances numerous factors to achieve optimal performance. At S.B. Weston we can produce, manufacture and maintain moulds through their production life. Our toolmakers will consider material properties, component design, cooling efficiency, and ease of maintenance to produce high-quality, cost-effective moulds enabling us to manufacture a wide range of plastic components to meet diverse industrial needs. We’re here to advise and assist, so if you have a requirement for injection mould tooling then get in touch!